Streamlining Electronics R&D with TITAN's Advanced Testing Features
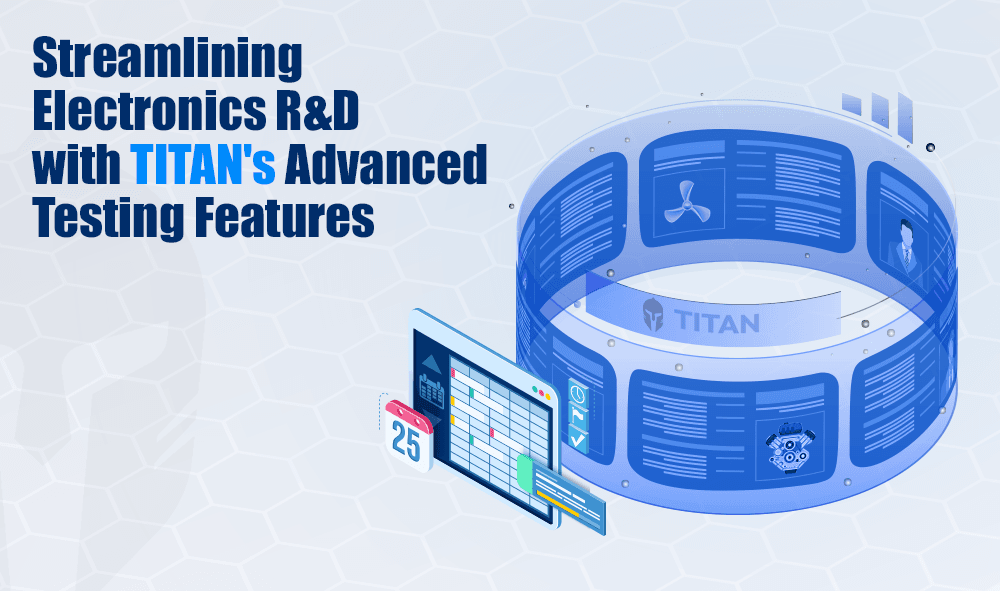
In the dynamic world of electronics manufacturing, quality isn’t merely a desirable attribute -- it's critical for achieving market success and maintaining customer trust. Manufacturers are constantly challenged to innovate rapidly while ensuring that their products withstand everyday use.
Enter TITAN: the adaptable verification and validation platform designed to bolster manufacturers' confidence in their products. By integrating TITAN into their research and development process, manufacturers can effectively reduce the risk of product recalls and protect their brand reputation, ensuring that each product meets stringent durability standards before reaching the market.
Streamline Development Process with Development Templates
The Development Template is a repository that defines the fundamental elements of a product line's and captures the associated requirements, risks, test cases, and test templates within the Titan environment. Once a Development Template is established for a product or model, the user can create a project for a specific variant or model year of the product line and import the Development Template components into the project. This approach enables users to quickly develop new projects for planning and executing a new model year or design iteration.
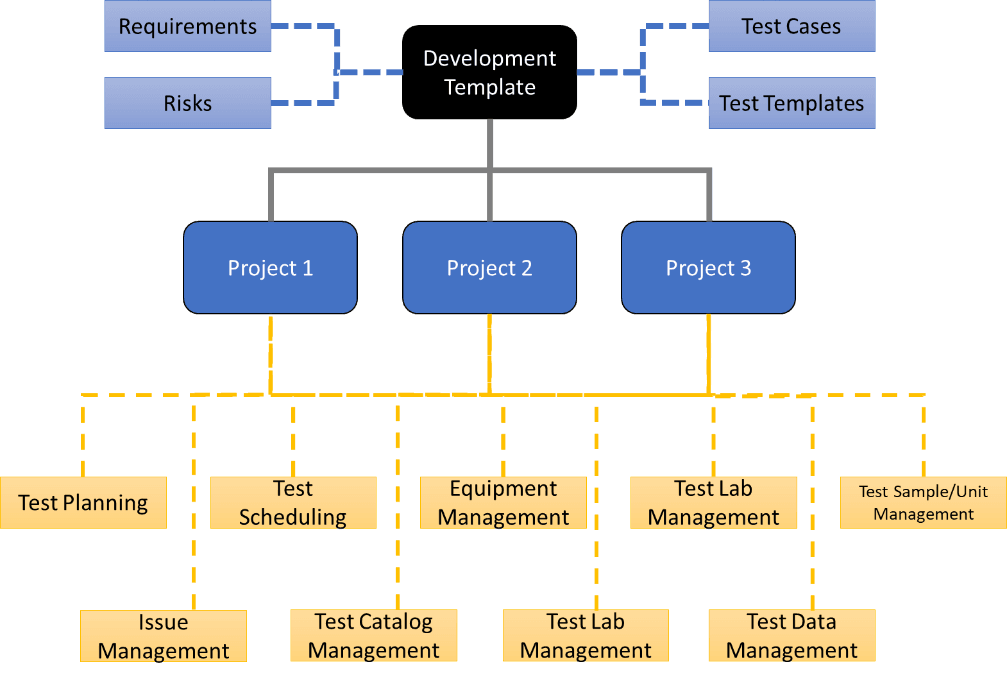
End to End solution for Design Verification Plan and Report
The Design Verification Plan and Report (DVP&R) is a structured tool used to plan, execute, and document the tests and analyses necessary to validate a product's design. It is the blueprint for ensuring that a product not only aligns with its intended design but also adheres to regulatory standards and performs as expected.
Titan simplifies the process of creating and collaboration on a DVP&R
Test Coverage
TITAN excels in this aspect by providing a clear view of the percentage of test coverage achieved. This helps ensure all critical aspects are thoroughly tested, reducing the risk of design flaws going unnoticed.
Schedule and Progress
TITAN simplifies this by enabling teams to define start and end dates for each testing activity. Monitoring the percentage completion for each phase allows stakeholders to assess whether the project is proceeding as planned.
Test Procedures
TITAN facilitates the tracking of test cases and procedures, including documenting steps, expected results, and required inputs for each test. This level of detail ensures precise testing execution, minimizing errors and enhancing result reliability.
Test Results
TITAN provides a platform for capturing test case results, including status, defects or issues identified, and related comments, notes and attachments. This information is invaluable for evaluating the product's performance against predefined acceptance criteria.
Defects and Issues
TITAN simplifies this task with a robust defect and issue tracking system. Teams can record detailed defect information, including description, severity, priority, status, and related comments or notes, ensuring prompt and systematic issue resolution.
Simplifying Report Generation
TITAN streamlines test reporting by automating data compilation and formatting. It stores all relevant data throughout the test's lifecycle, including preparation info, test conditions, inspections, facility, and equipment details. Engineers can maintain test report templates, ensuring efficiency and consistency. TITAN's checklist feature facilitates information capture and reuse, guaranteeing 100% repeatability. With TITAN's centralized knowledge repository, holding the test data and reports, organizations can effectively harness semantically rich data to pursue data-driven engineering.
Predictive Insights and Historical Data Analysis
TITAN’s ability to provide predictive insights and analyze historical data is also notable. By analyzing past test data, manufacturers can forecast potential failure points and assess how various design changes impact product durability. This predictive analysis helps R&D teams focus on design and material choices that boost product robustness.
Conclusion
Adopting TITAN for electronics testing equips manufacturers with a robust tool to enhance product reliability and testing efficiency. With capabilities like:
- Comprehensive Test Article Management: From fabrication to disposal.
- Intuitive Inventory Management: Ensure a consistent supply of consumable parts.
- Equipment Management and Tracking: Oversee all equipment details, from maintenance history to specifications.
- Advanced Lab Scheduler: Streamline reservations for facilities, equipment, test articles, and personnel.
- Work orders Management: Efficiently manage and track work orders to keep your operations running smoothly.
TITAN offers a holistic solution that not only simplifies verification and validation but also integrates quality throughout the product lifecycle.
Request a demo and see it Titan in action