Need For Prototype Vehicle Management System
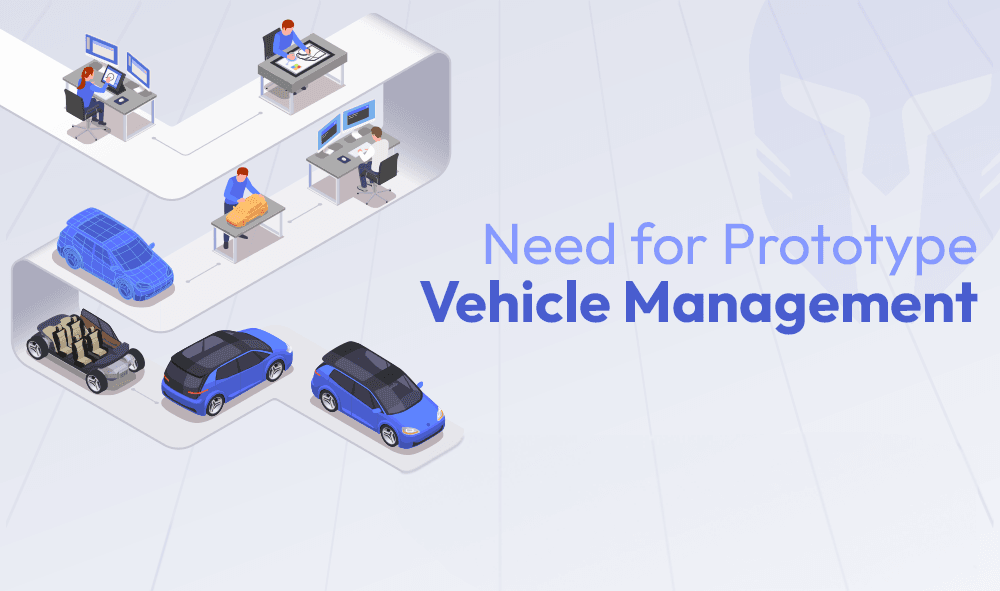
Prototype testing has been around for as long as humans have been inventing. Creating the best version of a tool requires trial and error, and without testing, end users will be left with a product that may not perform as intended and/or one that may cause injury. Unexpected issues that engineers and designers do not anticipate will undoubtedly crop up during prototype testing; nowhere is this more true than in the automotive industry. Auto manufacturers need to perform comprehensive prototype vehicle testing to ensure passenger safety as well as overall vehicle quality.
As additional technology is incorporated into automobiles, prototype testing has taken on an even more important role within the automotive industry. The entirety of prototype testing process and management needs to be done correctly and timely, since prototype vehicles are incredibly expensive to manufacture. In fact, some of the most complex prototypes cost up to $200,000. Understandably, managing the testing of these valuable assets is a priority, but it is a surprisingly tricky process.
Why is it so difficult to manage the entire process?
Many would think that the automotive industry would have worked out all of the kinks in the prototyping testing process by now. However, that is far from the case. There are countless groups and individuals involved throughout the scope of the prototype testing. With so many moving parts, it isn’t surprising that the automotive industry has not developed an effective solution for prototype testing management. But because of this, the industry continues to face a number of issues that have not been properly addressed.
Why is it so Difficult to Manage Prototype Testing?
One of the biggest challenges that car manufacturers, OEMs, and testing groups face is that it is extremely difficult to track the history of the prototype vehicle part changes and the testing performed — let alone which group currently has the prototype. There is no universal tool that manufacturers, OEMs, and testing facilities can all collaborate on. As a result, these groups wind up using varying tools to keep track of the history and changes made to the prototype.
In some cases, teams may be forced to look at old emails to try and track down where the prototype is located and what changes were made. This confusion and lack of communication can lead to additional problems during the testing process. If testing groups are unable to locate the prototype, groups may be sitting around ready to test the prototype wondering where it is. Additionally if testing groups are unaware of changes made to the prototype, they may have to scramble to adjust their testing protocols. This lack of collaboration and refusal to adopt modern methods of communication and tracking could compromise the entire timing of the prototype testing program.
For an industry that actively embraces technology and innovation, the prototype vehicle testing management process has been stuck in the stone age for decades.
One way to solve many of these problems would be to build more prototypes. The issue is that costs would quickly skyrocket. Companies would spend key resources building multiple, unnecessary prototypes when there is a much more effective solution. 12th Wonder has developed a comprehensive software platform that tackles the key issues discussed. Instead of wasting time and resources the automotive industry has a new tool to handle prototype testing management.
TITAN Simplifies Prototype Test Management
TITAN application was developed using years of experience working within the automotive industry. 12th Wonder took the problems that the industry was experiencing and built a platform to alleviate them. The application is able to manage the vehicle prototype testing process from the build process to until it is either destroyed or retired.
Teams across groups and organizations will be able to use the same tools in order to keep track of the history, part changes, service history, test history, issues and current location of the prototype vehicle. Instead of relying on Excel or pen and paper, teams will be able to collaborate with TITAN application. Users can easily enter all the necessary information related to testing, which enables concurrent users to access information instantly. The changes that are made to the prototype vehicle during the testing process, inspections and maintenance will be well documented. Engineers can use the data to make better decisions, and can have faith that the data is accurate.
All testing and maintenance data, from crash rating testing to rear axle lifecycle testing, will be kept in one convenient place for all collaborators. Information silos in regards to prototypes will be effectively eliminated, and no departments will be left in the dark. If a prototype part needs to be replaced, OEMs and testing centers can stay on the same page in real time. TITAN improves the traceability, visibility, and efficiency of the entire prototype testing process. Overall, TITAN transforms the prototype vehicle management pipeline. TITAN takes all of the guesswork out of the decision-making process.
Managing vehicle prototype tests becomes a much simpler process with TITAN. Your team and collaborators will work better than ever to test prototypes that translate into vehicles that consumers love and trust. 12th Wonder can provide the necessary customization to ensure that your testing processes run smoothly.
To Know more about TITAN and prototype vehicle management, schedule a demo.
Request a demo and see it Titan in action